Rapid prototyping is the best iterative approach during the design stage of a product. The objective of this technique is to quickly make the necessary improvements on the design using the prototypes that can be made in multiples and short cycles.
With rapid prototyping, product designers and developers can perform tests to check the components’ fit and function. It can help bring the product to the market earlier than its competitors as adjustments in the materials, shape, size, color, manufacturability, assembly, and many others can be done based on the results of testing and evaluation.
There are several rapid prototyping processes and it continues to evolve because product designers are trying to determine which technology or process best suits their unique application. This begs us to question, how does a product designer determine the right prototyping process?
This article will explore the pros and cons of various rapid prototyping techniques commonly used by product designers. Its ultimate goal is to help you determine which process applies to your product cycle.
Comparison of Some Common Rapid Prototyping Techniques
Stereolithography (SLA)
This technique is a form of additive manufacturing. It builds parts with a pool of UV-curable
section of the part on the surface. The process is repeated multiple times until the part is completed.
- Advantages: It is best suitable for cosmetic prototypes, concept models, and complex designs since the process can produce complex geometries and has excellent finishes.
- Disadvantages: The parts formed from this process are not as durable as those made from engineering-grade resins.
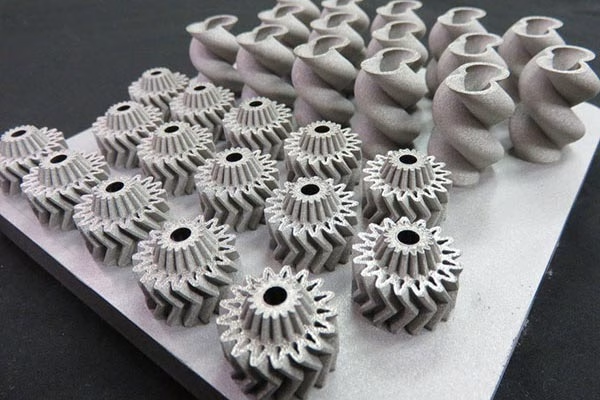
3D printing products
Selective Laser Sintering (SLS)
In the SLS process, the CO2 laser draws on a hotbed of nylon-based powder, from the bottom up. The material fuses to form the design. It is repeated until the whole component is formed. SLS can create parts with complex geometries and do them in large volumes. By far, this is one of the few processes that create durable products.
- Advantages: The parts made from SLS are durable and suitable for functional testing.
- Disadvantages: It does not produce a smooth finish. Most of them have a grainy or sandy texture.
Direct Metal Laser Sintering (DMLS)
DMLS is a variation of additive manufacturing that can produce metal prototypes for functional and end-use parts. The process is almost the same as SLS, only this time the material is metal in powder form. As the power is drawn to the surface, it fuses to form a solid part.
Advantages: DMLS produces prototypes that are strong as they are denser and ready for functional testing or as end-use parts.
Disadvantages: Production cost for the process can be high for multiple parts.
Fused Deposition Modeling (FDM)
This prototyping technique uses the extrusion method to melt and solidify the thermoplastic resin material into a prototype. It can be ABS, polycarbonate, or a combination of both. The prototype made from this process can be used only for functional testing.
- Advantages: FDM-made prototypes are not too pricey and yet they are strong enough for functional testing.
- Disadvantages: The finished parts from FDM have a poor surface finish and with pronounced rippled characteristics.
Computer Numerically Controlled Machining (CNC)
The most familiar type of rapid prototyping is CNC. In this process, a block of metal or plastic is clamped into a CNC mill or lathe and cut into a finished part using a subtractive process. The finished part has superior strength and excellent surface finish compared to additive manufacturing.
- Advantages: The machined parts have good surface finishes and are stronger since they are made from engineering-grade metals and thermoplastics.
- Disadvantages: There are some limitations in the geometry, and the production cost is more, especially when done in-house.
Injection Molding (IM)
This process works by injecting the material (thermoplastic resins) into the mold, which is very much the same as in high-volume production. Why does it belong here? The process is considered rapid because instead of using the traditional steel for tooling, it uses aluminum.
- Advantages: The molded parts from the different engineering-grade materials have an excellent surface finish. It can also serve as a gauge for the manufacturability of the design.
- Disadvantages: IM has additional initial tooling costs.
Conclusion
Prototype models can help the design team in decision-making by allowing functional and form testing. The data from the testing and analysis can help prevent potential manufacturing issues during the production phase. To determine the best rapid prototyping process, you need to know what you want to accomplish.