Injection molding might sound like an intimidating industrial process, but it’s the backbone of countless products you use daily. From your smartphone case to your car’s dashboard, injection molding is vital in modern manufacturing. Let’s break down this essential process and explore why it’s the go-to choose for high-volume production with exceptional precision.
What is Injection Molding?
Injection molding is a versatile manufacturing technique that involves the injection of molten material into a specially designed mold. This process can utilize various materials such as plastics, metals, and ceramics. The molten substance is carefully injected into the mold, where it cools and solidifies, acquiring the precise shape of the mold.
Once the cooling process is complete, the mold opens, releasing the newly formed part. This part can be utilized directly or undergo further finishing as needed. The adaptability of injection molding makes it suitable for producing various components across various industries, contributing to its widespread use in modern manufacturing.
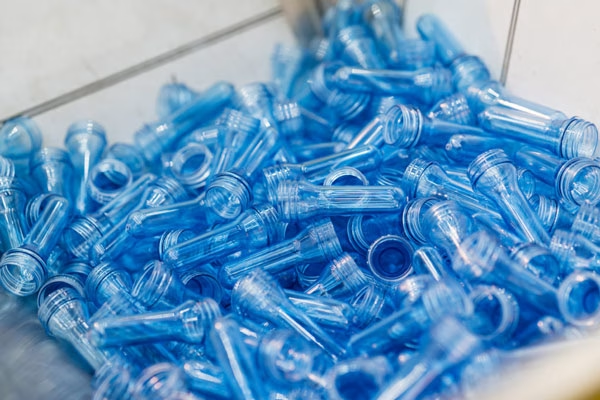
Plastic parts
Why Choose Injection Molding?
- High-Volume Production: Injection molding is the king of mass production. Once the mold is created, it can be used to rapidly produce thousands, even millions, of identical parts. This efficiency is a game-changer for businesses that need to meet large-scale demands.
- Unmatched Precision: The molds used in injection molding are incredibly precise, often machined to thousandths of an inch tolerance. Every part produced is virtually identical to the last, ensuring consistent quality and performance.
- Complex Geometries: Injection molding excels at creating intricate shapes and complex designs. The molten material can flow into even the tiniest details of the mold, allowing for intricate features that would be difficult or impossible to achieve with other manufacturing methods.
- Material Variety: Injection molding can use a wide array of materials, from everyday plastics like polypropylene and ABS to high-performance engineering plastics and even metals. This versatility makes injection molding suitable for a diverse range of applications.
- Cost-Effective at Scale: While the initial mold creation can be an investment, the per-part cost of injection molding decreases dramatically as production volume increases. This makes it a cost-effective choice for mass-produced goods.
NICE Rapid: Your Injection Molding Experts
At NICE Rapid, our passion lies in the intricate fusion of art and science that is injection molding. Our team comprises seasoned engineers and technicians well-versed in harnessing cutting-edge equipment to deliver top-tier injection molded components tailored precisely to your specifications.
Our versatility caters to a wide spectrum of needs, ranging from meticulous prototype creation for rigorous testing to efficient execution of full-scale production runs. Regardless of the complexity or scale of your project, we possess the expertise and capabilities to guide it seamlessly from the initial conceptualization phase to its triumphant completion.
Our unwavering commitment to excellence ensures that every step of the process is executed with precision and care, resulting in injection molded parts that meet and exceed your expectations.
Ready to Harness the Power of Injection Molding?
Injection molding isn’t just a manufacturing process; it’s a pathway to bringing your product visions to life efficiently and with unparalleled precision. Contact NICE Rapid today to explore how injection molding can revolutionize your production process and open up new possibilities for your business.