The automotive industry is highly competitive. Automotive manufacturers are caught in a never-ending quest to improve vehicle performance while reducing emissions. Weight is a considerable factor in vehicle consumption, and reducing weight helps to lower CO2 emissions and improve performance.
Pressure die casting is a critical production method used by automotive manufacturers to produce strong, lightweight components in a range of highly resilient materials. This manufacturing process utilizes molten metal materials to create high-quality parts used in automotive mass manufacturing.
Using High-Pressure Die Casting (HPDC) allows manufacturers to create components ranging from gearboxes to gears. It’s a common process used to produce small to mid-sized vehicle components.
This post looks into the use of HPDC in automotive manufacturing processes. We’ll discuss the benefits and drawbacks of this method to give you an idea of why it’s an industry standard.
Pressure Die Casting Processes in the Automotive Industry
HDPC promises manufacturers plenty of benefits for designing and producing high-volume vehicle components. Large die-casting processes allow for replacing 70 to 100 components with a single part. This effect reduces production time and reduces the complexity of production processes to cut costs.
HPDC utilizes high pressure and fast speed in its production processes, allowing for the cost-effective casting of metal parts for vehicles. HDPC has a reputation for consistency and accuracy in production processes, with the ability to produce parts at high volumes with repeatable precision quality.
HDPC is different from gravity die-casting. Gravity casting involves the use of molten metal vertically poured into a casting mold. Pressure die-casting processes are automated, and the material is injected into a hardened steel die.
The automated features of this production method make it highly suitable for mass production requirements. HPDC is ideal for the automotive industry but is also a common manufacturing method used in aerospace components manufacturing and in electronics and hardware production applications.
What are the advantages of pressure die casting?
There are several advantages to incorporating HPDC processes into automotive component manufacturing.
- Excellent precision manufacturing and high accuracy.
- Suitable for producing large volumes of identical components.
- Cost-effective for large production volumes, lowering unit costs.
- Fast production times due to the fast curing of molten metal into its final solid form.
- Suitable for millions of production cycles before requiring tooling replacement.
- Ideal for the production of a wide range of components.
- An excellent choice for manufacturing complex automotive components.
- Suitable for mass-manufacturing processes with high-volume production requirements.
- Excellent dimensional control and surface finish.
- Allows for electroplating of finished components.
- Ideal for the production of lightweight components with thin walls.
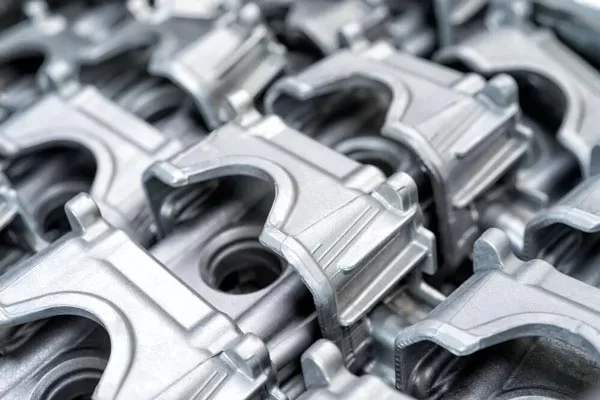
Automotive parts
What are the disadvantages of pressure die casting?
While there are many advantages to incorporating HPDC into automotive manufacturing processes, there are a few drawbacks.
- Expensive setup costs for tooling and materials.
- Requires a significant capital investment into equipment.
- Inflexible compared to other processes like gravity casting.
- Not suitable for rapid prototyping projects due to high development costs for one-off parts.
Materials for Die Pressure Casting in the Automotive Industry
Automotive part manufacturing features many different materials used in the production process. Some of the common alloys featured in HDPC manufacturing processes include the following.
Aluminum
The most commonly used material in HDPC manufacturing processes. Aluminum is the primary material used in this alloy and is also suitable for use as an additive in other materials. Adding this material to other alloys may alter its properties, improving the performance of HPDC parts. Aluminum features excellent heat-transfer properties, low production costs, and excellent surface finish.
Zinc
Zinc is the most popular choice for HDPC processes. It’s ideal for manufacturing dies for high-volume production processes. Zinc offers excellent strength, superior surface finish, and excellent corrosion resistance for finished parts.
Magnesium
This material features in alloys where strength and durability are top concerns. It’s commonly added to other alloys to improve strength. Magnesium alloys are the ideal choice for manufacturers working with high-temperature tooling requiring a fast-cooldown process after completing the casting process.
The Advantages of Using Die Pressure Casting in the Automotive Industry
Some advantages of using HPDC processes in automotive components manufacturing include the following.
Lightweight Components
One of the key reasons for the rise in popularity of HDPC processes in automotive manufacturing is its ability to create lightweight parts. Other production methods might offer faster production times or lower cost-per-unit advantages.
However, HDPC offers manufacturers the advantage of reducing weight in final components, improving consumption, lowering emissions, and improving vehicle performance. Manufacturers benefit from the lightweight design and construction of their vehicles. It reduces shipping and production costs, leading to savings on production and logistics costs for the manufacturing brand.
Casting automotive components with HPDC processes allows automotive manufacturing brands to improve efficiency, reducing waste in manufacturing processes.
Increased Flexibility & Automation
HPDC components are ideal for use in the mass manufacturing vehicles and automotive components. It allows for high-volume production, allowing manufacturing brands to benefit from economies of scale in their processes.
HPDC parts include suspension components, chassis, body panels, and cast wheels. It’s suitable for mass manufacturing and custom car design. HDPC is ideal for producing vehicle components or spare parts.
Enhanced Productivity
HDPC offers vehicle manufacturers better efficiency with their processes. The result is a drop in labor costs in manufacturing, allowing automotive brands to remain competitive in the market.
For instance, HDPC manufacturing processes for wheel production allow manufacturers to produce four times as many wheels as with manually assisted production methods.
In Closing
High-pressure die casting offers automotive manufacturers plenty of advantages over conventional manufacturing methods. HPDC is a relatively new technology in the industry, but manufacturing brands like Tesla are successfully incorporating it into their manufacturing process.
We can expect automotive manufacturers to greatly influence the advancement of this technology in the future. By implementing the HPDC process into their manufacturing, automotive brands will save on production time, minimize waste, and reduce costs.
HPDC offers manufacturers a win-win scenario for their business. It drops the production cost of cars, allowing manufacturers to use these savings to attract price-sensitive buyers and improve their brand presence in the market.