5 Most Common Resins Used in Plastic Injection Molding
One of the reasons Plastic Injection Molding is so prevalent among the manufacturing processes is due to it offers a wide range of materials selection. This allows product designers and engineers able to create unique parts that could meet their strict specifications and application. Each resin has different qualities, strength and weaknesses. Understand each resins’ materials and mechanical properties will help designers to identify which resin best suit their certain jobs or applications.
This article is designed to provide more in depth understanding on the 5 most common plastic materials for injection molding.
1. ABS
Acrylonitrile Butadiene Styrene (ABS) is a thermoplastic polymer made from the chemical bonding of three monomers: acrylonitrile, butadiene, and styrene. The proportions of each monomer are adjustable, but styrene typically made up 50% of ABS, the rest are the combined amount of acrylonitrile (15% – 35%) and butadiene (5 – 30%).
Pros:
- The advantage of ABS is the ability to modify the composition of ABS, which allows manufactures to create part with a variety of properties.
- Strong, stiff and offer good impact resistance.
- Relatively inexpensive and easy to process.
- Can be easily machined, sanded or colored.
Cons:
- Not a right choice for applications where flexibility is required.
- Low resistance to creep, especially at high temperature.
Application:
- Consumer products such as laptop housings, luggage, battery cases, toys and piping.
- Automotive components such as dashboard padding in cars and insulating panels.
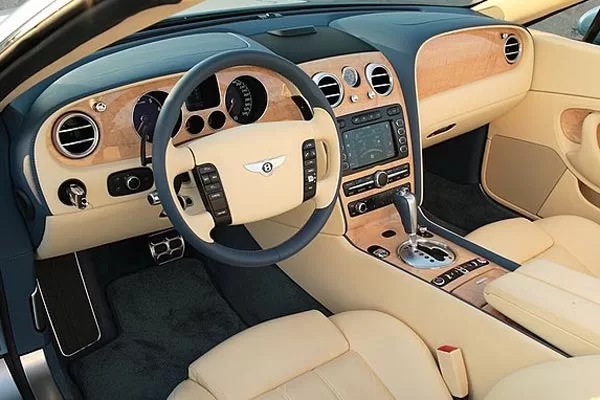
2. PP
Polypropylene (PP) is an economical thermoplastic polymer used in a wide variety of applications. It has the lowest density of all thermoplastics.
Pros:
- Very lightweight.
- High flexibility and very versatile. It’s ability to retain its original shape without breaking makes it suitable as a living hinge. For example, it can be used as ‘snap-open-and-close’ bottle cap.
- Good resistance to chemical and solvents, which makes it ideal to be used as dishwasher-safe containers or other chemical formulation containers.
- Low water absorption, which makes it a good choice for items that are exposed to moisture.
- Tough, durable and heat resistant.
Cons:
- Should not be used in high temperature applications.
- Not easily to be glued or painted.
Application:
- Automotive industry, such as bumper beams, door panels and structural components.
- Consumer goods such as containers for food and chemicals.
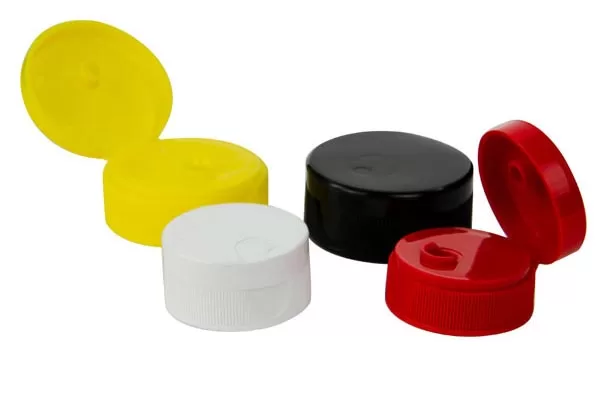
3. PA
Polyamides (PA) or Nylon is the most common thermoplastic polymers. It is widely used in plastic injection molding and in applications that require stronger mechanical properties and higher temperature tolerance than Polypropylene (PP). It is used in many applications from consumer goods to aerospace. Nylon polymers can be mixed with a wide variety of additives to achieve varying properties.
Pros:
- Very strong and lightweight.
- Resistant to abrasion and chemicals.
- Very flexible.
Cons:
- Poor resistance to heat and moisture.
- Takes a very long time to biodegrade.
Application:
- Medical products
- Automotive products
- Sports equipment
- Footwear and clothing
- Industrial components
- Consumer parts
- Aerospace components
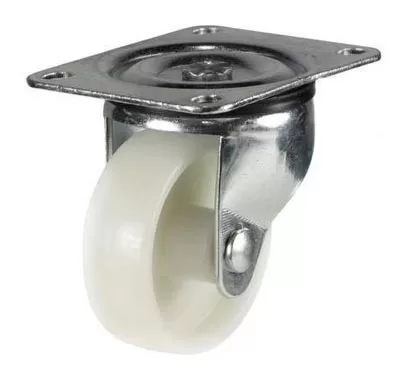
4. PC
Polycarbonates (PC) are a group of lightweight thermoplastic that are easily processed and molded.
Pros:
- High heat resistance and impact strength, which makes them ideal for products exposed to high temperature and impacts, such as safety helmets.
- High transparency of some PC grades allows for the use in optical products.
- High creep resistance.
Cons:
- Not suitable for application where higher material flexibility is desired.
- Not ideal for heavy solvent exposure.
Application:
- Cameras
- Eyeglasses
- Safety goggles
- Beverage dispensers
- Medical or lab application such as beakers, test tubes, etc.
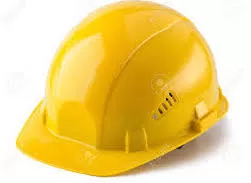
5. PE
Polyethylene (PE) is a semi-crystalline thermoplastic that is inexpensive and adaptable to many processing methods. It is one of the most versatile and most widely used plastics in the world. The crystalline regions of PE molecules can vary, resulting in high-density polyethylene (HDPE) or low-density polyethylene (LDPE).
Pros:
- Resistant to moisture absorption.
- High ductility, tensile strength and impact resistance.
Cons:
- Susceptible to stress cracking
- Poor UV resistance
- Poor temperature capability
- Flammable
Application:
- Plastic bags
- Plastic films
- Plastic bottles
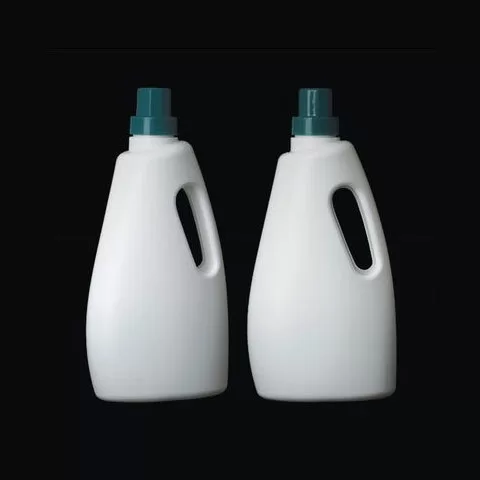