Three Main Benefits of Using LSR Molding
Liquid silicone rubber (LSR) molding is a popular manufacturing process that offers many benefits over traditional injection molding. LSR is a two-part process that uses a platinum-cured silicone mold and a Reaction Injection Molding (RIM) system.
The main advantage of LSR molding is that it can produce parts with intricate designs and tight tolerances. In addition, LSR molding is much faster than traditional injection molding, which makes it ideal for high-volume production runs.
However, LSR molding also has some disadvantages. The main drawback is that it is more expensive than traditional injection molding. LSR molding is not well suited for large or complicated parts
Important Benefits of LSR Molding
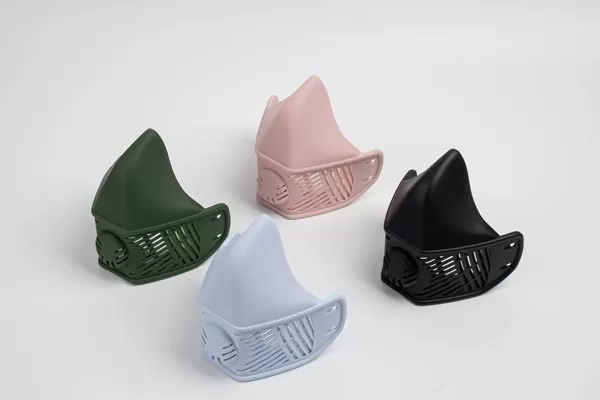
Many manufacturers have been using innovative technology (LIM) to create liquid silicone rubber injection molding (LSR). While exceedingly practical and effective, this molding technique is also quite complicated and prone to mistakes if not done correctly.
Silicone rubber products using the injection molding process provide cost-effectiveness and consistency for several applications across different industries. To know why this manufacturing process is important, here are its benefits:
1.Cost-effective yet produces quality seals and parts
While the LIM procedure is speedier and more affordable than other molding techniques like compression or transfer molding, it is more intricate and accurate. Additionally, LIM may be entirely automated, which requires less workforce and lowers labor expenses. Thanks to automation, which accelerates the procedure, cycle times may now be calculated in seconds rather than minutes.
LIM is also simple to repeat, which is advantageous for producing complicated components of excellent quality. LIM allows for the speedy and economical construction of a wide range of parts and seals, from tiny custom-shaped components to full vehicle body panels. This procedure’s adaptability and accuracy enable producers to produce high-quality components in the lowest amount of time.
2.Liquid silicone rubber offers great sealing benefits
LSR is the best option for many sealing applications because of its many dependable characteristics. It offers excellent resistance to ozone, water, weather, and temperatures that range from -65°C to 200°C. The resulting product has high resistance capabilities because of injection molding using this material.
Because it may have a low compression set with a wide variety of durometers, silicone is a material that works well with the LIM process. In addition, LSR materials are highly suited for the medical sector because of their flexibility in the durometer range.
3.The process has little waste of contamination
The LIM process, being a closed system, prevents contamination of raw materials from environmental exposure. As a result, LIM components and seals can be utilized for more demanding applications with less contamination, particularly in the medical sector.
Custom forms may be produced using rubber injection molding with minimum flash or rubber waste. The additional thin layer of material that exceeds the typical component geometry is called “flash.” Tool damage, excessive injection speed, or a weak clamping force are all potential causes of this. Flash and other waste are decreased with LIM automation and accurate applications.
LIM technology offers consistency and cost-effectiveness for many applications, notwithstanding any acknowledged disadvantages. With quick turnaround times and affordable pricing, liquid silicone injection molding technologies provide high-quality silicone components and seals.