Plastic injection mold is perhaps the most popular manufacturing process. The number of products made from this manufacturing process is plenty, which attests to how this process is critical in developing consumer products.
The injection molding process is the best way to manufacture products made from plastics. To better understand why injection molding becomes the most popular manufacturing technique, we go down to the basics. We have to know the processes involved in turning a design into a finished product through injection molding.
Step 1: Designing the Product
The first step to creating any product is designing. In the design process, the manufacturer can avoid costly mistakes later on. The main goal in this step is to design a product for aesthetics, function, and manufacturability, assemble, and so forth. A good design is something that satisfies these objectives, and it takes a lot of creativity to come up with this.
Nowadays, product designs are made through computer-aided design software. The best CAD software can allow for product iterations and prototyping for design evaluation. Some of the factors to consider when designing a prototype is the wall thickness and avoiding stress on the design like sharp corners.
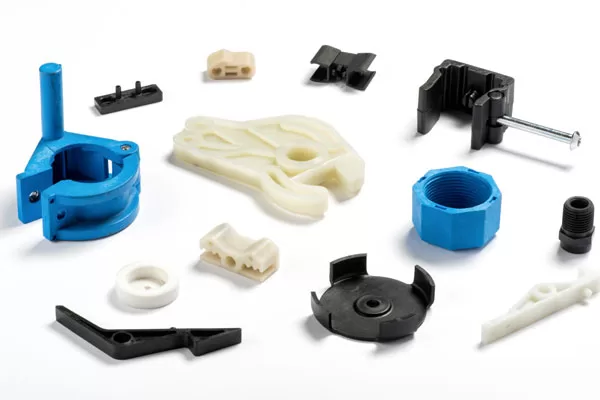
Plastic parts
Step 2: Designing the Mold
After rapid prototyping and product evaluation, the design is tested for form and function. During this stage, various revisions are made until the design is ready for production.
The next process will be designing the mold for the injection process. There are several types of metals used to make the mold. Here are some of the possible choices:
- Hardened Steel – it may be the most expensive but the molds made from hardened steel can last longer.
- Pre-Hardened Steel – it may not last as long as hardened steel but it is the next best thing because it’s less expensive.
- Aluminum – this is used mostly for tooling for a prototype where only a small quantity is needed for testing. It is more appropriate for low-volume production.
- Beryllium-Copper Alloy – this type of material is commonly used for molds that need faster heat removal or where shear heat is concentrated.
Like in designing a product, designing a mold is also necessary because it provides the opportunity for the product development team to avoid defects during the plastic injection molding process. The main factors to consider when choosing a mold material are the number of cycles needed and the material of the finished product.
Step 3: The Manufacturing Stage
After designing the product, testing, approval, and designing the mold, the plastic injection process is about to be completed with the actual production. Some of the essential points in the injection molding process include:
- The plastic material, which comes in granular form, goes into the heating barrel.
- Once inside, the plastic is heated to a predetermined temperature.
- The melted plastic is injected into the mold.
- When the mold is filled with material, it will undergo curing.
- After curing the mold will open and eject the part.
- This cycle will be repeated to fulfill the requirements.
The plastic injection molding process is very fast. It can manufacture hundreds of thousands of products in a matter of days.